Making the Earth
More Stable
Questions and Answers
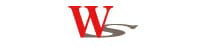
We’ve listed a few of the most frequently asked questions about Asphalt Pulverization Recycling , along with their answers, below for your convenience.
Email Us your questions!
You are welcome to call us with your questions: 707-678-0369.
Soil Stabilization
Stabilizing permanently alters the soil upon which you are going to build. It improves the soil’s r-value and its sheer and unconfined comprehensive strengths, and lowers the soil’s permeability to water. With stabilization, you gain structural value which, ultimately, saves you time and money. Soil stabilization eliminates the need for digging out and replacing; and it reduces the amount of base and final application materials which would be needed to achieve the same results. Western’s Soil Stabilization is value engineering at its best.
No; the materials used are dictated by the soil on your jobsite. For example, expansive clays need lime while granular soils need cement. The use of a trained and licensed geotechnical soils engineer is crucial to getting a proper mix design for your specific job. For examples of mix designs and MSDS sheets, please refer to our Technical Library.
Although this is done sometimes, Western Stabilization’s experience shows that an AB (aggregate base) layer acts as a barrier between the rigid stabilized soil and the flexible asphalt layer. This helps to prevent reflective cracking. As asphalt is porous, moisture drains into the AB, rather than sitting between the asphalt and the soil. See our Technical Library for some examples of typical stabilized asphalt sections.
Yes; once compacted and finished, the stabilized soil must be kept top-wet or oil-sealed until covered with rock or asphalt. This is crucial. Moisture must be retained within the treated soil until covered. If the soil loses too much moisture, it will begin to crack.
Because the pH of the stabilized soil is 10-1/2 (not conducive to vegetative growth), we carefully work around the landscaped areas. If landscaping is necessary in a stabilized area, topsoil can be placed on the surface and shallow-rooted plants can be grown. For bigger plants, large holes can be dug in the stabilized layer with fresh soil added to accommodate roots and to facilitate drainage.
Soil Stabilization raises the soil’s pH for only a short distance adjacent to the stabilized section. Because the calcium hydroxide in Western’s Soil Stabilization materials has only a limited solubility in water, its impact upon storm water run-off is minor. Not only is it diluted rapidly, it reacts with environmental carbon dioxide, clay minerals, and other organic substances contained in the run-off to become neutralized.
Winterization is the best decision you can make to ensure the success of your project. Jobsite delays cost millions of dollars in California. Under normal conditions, your jobsite would be delayed for weeks (and, possibly, months) after the rain stops. Even if you “rip” and incur the cost of trying to aerate the soil, you still lose a lot of precious time and money. Winterization allows you to get back on your site just 1-3 days after the soil is treated! Once treated, the soil is protected from future rains.
The most common misunderstanding about Winterization/Dry-Up is with regards to standing water. Dry-Up will take care of the muddiest conditions, but standing water must be pumped off first. Moisture is the reactive agent to lime, fly-ash and cement, so it would not be cost-effective to spend a lot of energy and money on standing water. After the rain stops, pump off the standing water, Winterize, and go back to work.
Because the pH of the stabilized soil is 10-1/2 (not conducive to vegetative growth), we carefully work around the landscaped areas. If landscaping is necessary in a stabilized area, topsoil can be placed on the surface and shallow-rooted plants can be grown. For bigger plants, large holes can be dug in the stabilized layer with fresh soil added to accommodate roots and to facilitate drainage.
Winterization/Dry-Up raises the soil’s pH for only a short distance adjacent to the stabilized section. Because the calcium hydroxide in Western’s Winterization materials has only a limited solubility in water, its impact upon storm water run-off is minor. Not only is it diluted rapidly, it reacts with environmental carbon dioxide, clay minerals, and other organic substances contained in the run-off to become neutralized.
Winterization/Dry-up
Winterization is the best decision you can make to ensure the success of your project. Jobsite delays cost millions of dollars in California. Under normal conditions, your jobsite would be delayed for weeks (and, possibly, months) after the rain stops. Even if you “rip” and incur the cost of trying to aerate the soil, you still lose a lot of precious time and money. Winterization allows you to get back on your site just 1-3 days after the soil is treated! Once treated, the soil is protected from future rains.
The most common misunderstanding about Winterization/Dry-Up is with regards to standing water. Dry-Up will take care of the muddiest conditions, but standing water must be pumped off first. Moisture is the reactive agent to lime, fly-ash and cement, so it would not be cost-effective to spend a lot of energy and money on standing water. After the rain stops, pump off the standing water, Winterize, and go back to work.
Because the pH of the stabilized soil is 10-1/2 (not conducive to vegetative growth), we carefully work around the landscaped areas. If landscaping is necessary in a stabilized area, topsoil can be placed on the surface and shallow-rooted plants can be grown. For bigger plants, large holes can be dug in the stabilized layer with fresh soil added to accommodate roots and to facilitate drainage.
Winterization/Dry-Up raises the soil’s pH for only a short distance adjacent to the stabilized section. Because the calcium hydroxide in Western’s Winterization materials has only a limited solubility in water, its impact upon storm water run-off is minor. Not only is it diluted rapidly, it reacts with environmental carbon dioxide, clay minerals, and other organic substances contained in the run-off to become neutralized.
Asphalt Pulverization Recycling
Asphalt Pulverization Recycling (also known as Full Depth Reclamation) is a recycling process. Recycling asphalt saves money, time and the environment. Why demo and pay to haul off and discard? You can pulverize in place, and then use the pulverized asphalt as new base material on-site or for a different job. We say, “Be wise. PULVERIZE!”
No; Pulverization is the technique by which the full flexible pavement section and a predetermined portion of the underlying base materials are uniformly crushed, pulverized or blended, resulting in a stabilized base course. Grinding (milling, cold planing) is the controlled removal of an existing pavement to a desired depth, longitudinal profile, and cross-slope. Normally, grinding is used for overlay work. In short, grinding takes a small amount off the top while Pulverization recycles the entire section.
Yes; the same equipment does both the stabilization and the pulverization. Please refer to our equipment page for more information.
No; there is machinery out there which can do this, but Western Stabilization does not perform concrete demolition.
We can pulverize up to 15 inches of asphalt in a single pass.
Yes; Western Stabilizations Asphalt Pulverization Recycling typically meets Class II specifications, depending upon the material.
Foamed Asphalt Recycling
Foamed Asphalt Recycling is a process in which the asphalt section is recycled in-place without the traditional application of heat during the process. The entire pavement section is pulverized, along with some of the underlying base material and hot liquid asphalt oil is injected with a small amount of water into the newly broken-up material. The foaming action expands the asphalt allowing it to encompass and stick to the pulverized particles and form a mortar that doesn’t harden immediately. While the foaming action takes place in 10-15 seconds, the newly foamed asphalt remains workable long enough to finish compacting, grading and rolling. Foamed Asphalt Recycling produces a high quality, strong and flexible product that is more environmentally friendly than traditional demolition and reconstruction. Foamed Asphalt Recycling rebuilds the roadway from the bottom up, which can virtually eliminate symptomatic problems such as reflective cracking and shallow base failures.
Recycling is more cost-effective than total reconstruction. Foamed Asphalt Recycling has been known to cut reconstruction costs by fifty percent. Foamed Asphalt lengthens the life of the finished product and decreases future maintenance considerably. Foamed Asphalt creates a flexible, non-expansive and fatigue-resistant base, with strength characteristics approaching those of cemented materials. Foamed Asphalt Recycling has a low impact on the public and surrounding businesses.
Yes; your Foamed Asphalt Recycling project must be engineered. For more details, please refer to our Technical Library.
Yes; in fact, Foamed Asphalt Recycling produces a more stable, durable base with a much longer life than traditional methods. Highway 20, west of Williams, is a good example of the permanence, efficacy and efficiency of Foamed Asphalt Recycling. Please see Projects for photos of Western’s Highway 20 job.
No; your Foamed Asphalt Recycling project will need a wear surface and an overlay.